The methodologies and tools developed are demonstrated on two industrial use cases, both equipped with an electric arc furnace and immersed in an urban context, producing different types of steel and therefore with different production processes: APERAM Châtelet and PITTINI Osoppo. These type of plants were selected as one of the noisiest in steelmaking production, and given their small size, they are more likely to be located near urban contexts.
FENO
Pittini Group which Ferriere Nord (FENO) belongs is a European leader in the production of steel long products for building and industrial applications. The manufacturing plants cover the whole production cycle: from raw material to the final product as wire rods and hot rolled reinforcing steel bars and coils. The wire rod is further processed to obtain electro-welded products for the building sector, meshes, and lattice girders, and drawn and cold rolled products for industrial application and welding wires.
The areas that cover the case study of SILENCE range from the scrap arrivals to the plants, its management until its melting:
- SCRAPYARDS: Annually, FENO processes over 1.7 Mtons of scrap materials. It boasts three indoor scrapyards spanning 22,000 square meters each, capable of accommodating up to 60,000 tons of scrap. On a daily basis, approximately 5,000 tons of scrap are handled, sourced primarily by train from overseas (constituting 60%) and by trucks from Italian companies (making up the remaining 40%). Furthermore, FENO benefits from additional storage capacity provided by an outdoor scrapyard, covering 12,000 square meters and accommodating up to 40,000 tons of scrap.
- EAF: with an annual production of over 1.4 Mtons, FENO’s Electric Arc Furnace (Figure 5) is able to perform more than 10,000 heats, as a batch process with an average tapped steel of around 148 tons. Daily 30-33 heats are performed with a production quantified in 4,400-4,800 tons.
Both internal and external phonometers are going to be installed throughout the plant to improve the current system based on a single internal phonometer installed close to the EAF plant: two new phonometers inside the EAF building, and three new phonometers outside are installed, close to the border of the scrap yard. The noise detected by these new sensors will be used to develop and train a ML system which, in turn, will help operations to decide which countermeasure to use to keep the noise levels suitably under control.
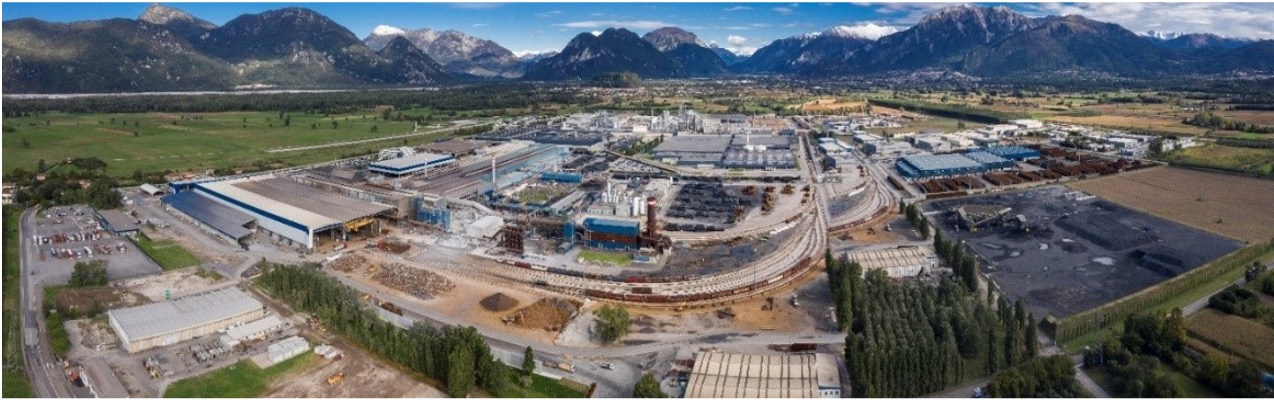
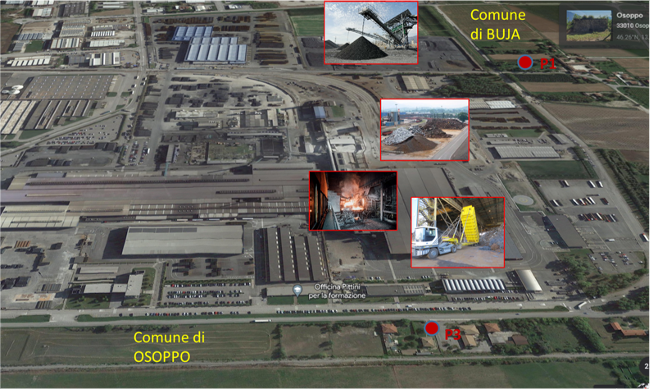
APERAM
Aperam Châtelet is part of an international group structured into four divisions, and it plays a strategic role in the production of flat stainless steel. The plant covers the full production cycle, from scrap reception to melting and refining, serving key sectors such as industry, construction, and transportation.
The SILENCE case study focuses on operations ranging from scrap delivery and handling to the electric melting process:
SCRAPYARDS: Aperam Châtelet receives and handles approximately 550,000 tons of scrap per year, including both carbon and stainless steel, sourced from within the group and international markets. The materials are delivered via truck (50%), barge (40%), and rail (10%), and sorted into 50 dedicated enclosures according to quality. The site’s total scrap storage capacity is 40,000 tons. This setup ensures a stable and efficient supply of raw materials to the melting process.
EAF: The Electric Arc Furnace (EAF) is the core of the steelmaking process at Châtelet. It melts about 170 tons of scrap per cycle, requiring approximately 70 MW of electricity and using wall burners to accelerate melting. The process takes around 60 minutes and uses 2 to 3 scrap baskets, depending on density. During melting, lime and alloying agents are added to form a slag that captures impurities and protects the refractory lining. The resulting "raw" steel is then refined through the Argon Oxygen Decarburization (AOD) process and adjusted in ladle metallurgy (MEP) to achieve precise chemical specifications and temperature control. While the EAF is designed for a capacity of one million tons per year, current average annual production is approximately 650,000 tons.
Five new acoustic sensors will be installed in different locations inside and out of the factory to allow for a continuous monitoring of noise levels in the plant area and nearby populated areas.
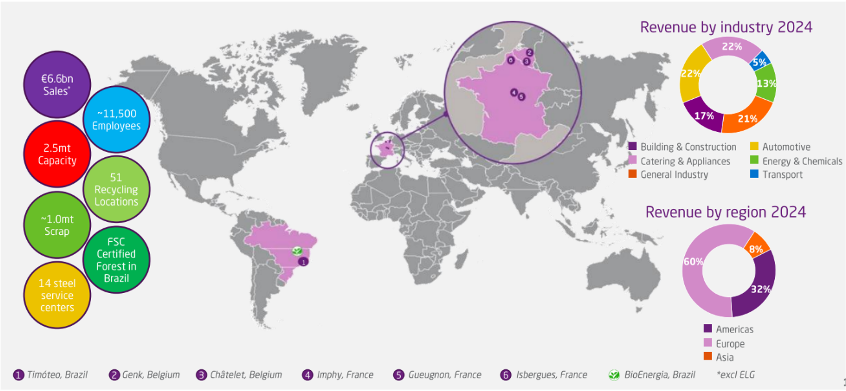
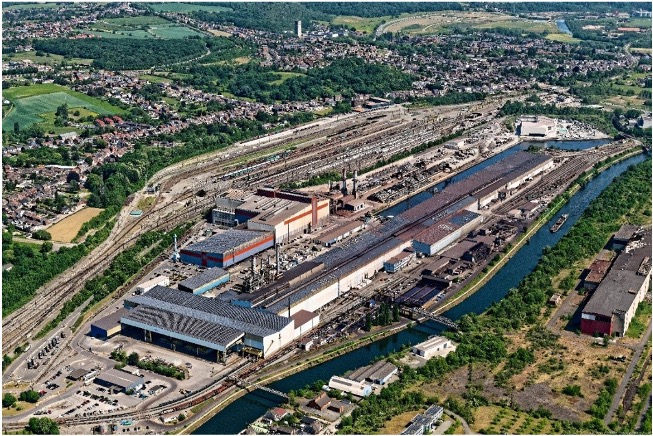